10+ Research Center
This institute focuses on understanding the molecular mechanisms of diseases into the developing new technologies.
Free Pick Up & Delivery
Free pick-up and delivery services are often offered by businesses to enhance customer convenience
24/7 Support Assistant
The support assistant is available 24 hours a day, every day of the week, ensuring continuous accessibility
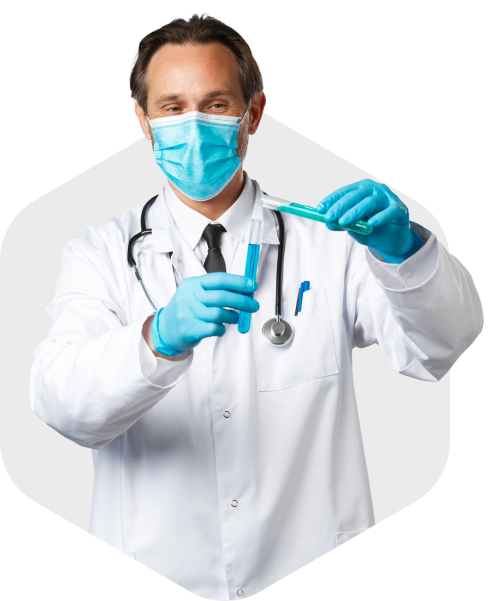
A combination of creative thinking and expertise
Industry leaders and business experts come together to start Darsh Labs and Research Pvt. Ltd. We are pioneer in the field of water testing, air testing and environment.
We take our job seriously to deliver you the most accurate and testing results as per the standard norms. We are committed to provide you the labs results for your business. Count on us for your quality control needs.
We test your water, air and environment!
Hours Generated
Tasks Completed
Worldwide Users
Projects Completed
We are willing to take bold action to achieve the extraordinary.
Water Testing
Water testing is a process of analyzing water samples to assess their quality and suitability for various purposes, such as drinking, industrial use, agriculture, and recreational activities.
NDT Testing
Non-Destructive Testing (NDT) Services are critical for ensuring the integrity, safety, and reliability of structures, components, and materials without causing damage or impairment.
Material Testing
Material Testing Services are the cornerstone of quality assurance and compliance across various industries, ensuring the reliability, safety, and performance of materials used in construction.
Coal & Minerals Testing
Coal & Minerals Testing Services play a pivotal role in ensuring the quality, purity, and compliance of these valuable natural resources. With our state-of-the-art laboratories and expert technicians.
Environmental Testing
Environmental Testing Services are essential for safeguarding public health, ensuring regulatory compliance, and mitigating environmental risks. Our comprehensive suite.
Soil Investigation
Our Soil Investigation Services encompass a range of techniques, from borehole drilling and soil sampling to laboratory testing and geophysical surveys.
Our Working Process
Client Briefs Project
The more details you can provide, the better lab can assist you
Lab Generates Proposal
Provide information on how the client can proceed with the proposal
Lab Start Testing
Specify the criteria for success and the key performance indicators
Reports Delivered
Our team is available for a follow-up meeting to discuss the contents
Blogs
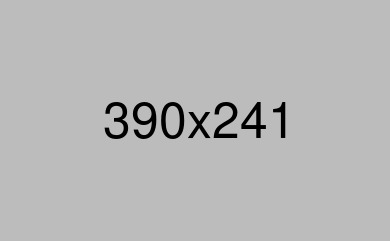
24Jun
Freshly Cosmetics Payments Makeover
The Information technology and software in development Problems solutions.
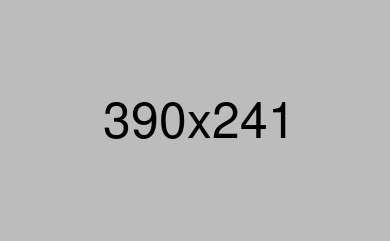
12Mar
Organic Chemistry Research Laboratory
Managing interactions customers throughout the entire customer lifecycle of the deal.
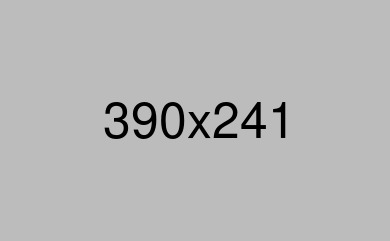
16Feb
The research team is filled with multidisciplinary
The systematic investigation and experiment to develop new products, processes improve